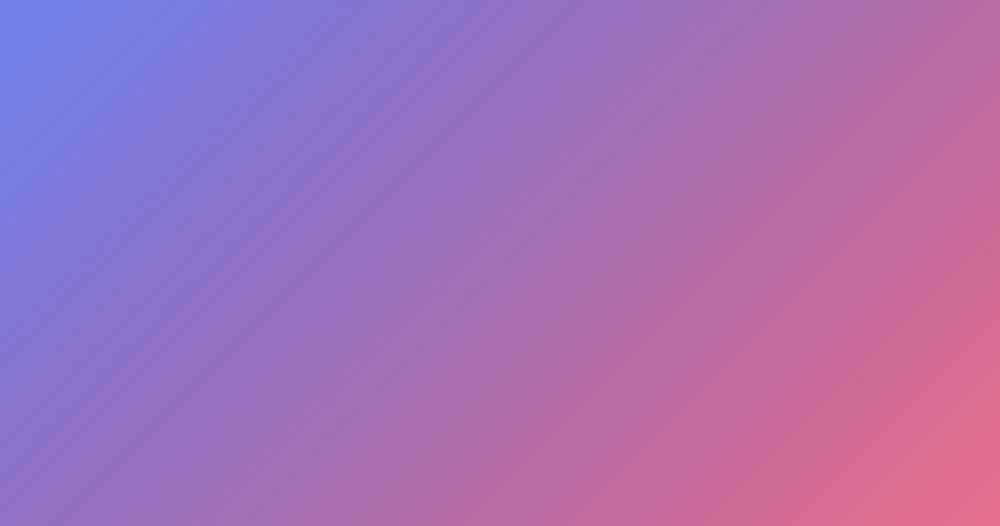
13
abrilRisk Assessment in Lean Manufacturing Projects
Risk management is an essential component of Lean Six Sigma projects|processes that aim to eliminate waste and optimize efficiency|operations that rely on identifying and mitigating risks|strategies that help organizations manage uncertainty and potential threats.
Importance of Risk Management in Lean Six Sigma Projects
Risk management is vital in Lean Six Sigma projects because it ensures that projects are completed on time and within budget. Project risks can include operational risks, reputational risks, or information security risks. Effective risk management helps to create a competitive advantage and drive innovation.
Steps Required for Uncertainty Modelling in Lean Six Sigma Projects
The following are the steps required for effective uncertainty analysis in Lean Six Sigma projects:
1. Identify Project Risks The first step in uncertainty management is to identify potential project risks. Techniques such as brainstorming, affinity diagrams, and SWOT analysis can be used to identify potential project risks.
2. Conduct a Risk Assessment Once potential project risks have been identified, gathered, or evaluated, they need to be assessed, evaluated, or analyzed. This requires a thorough understanding of the project's objectives and constraints.
3. Evaluate the Criticality of Risks Based on the risk assessment, evaluation, or analysis, risks need to be prioritized, ranked, or evaluated. High-priority, ranked, or critical risks should be addressed first, managed first, or mitigation strategies should be developed first, while low-priority, ranked, or critical risks can be addressed later, managed later, or mitigated later. This requires a thorough understanding of the project's objectives, constraints, and available resources.
4. Create Resilience Plans Once high-priority, ranked, or critical risks have been identified, assessed, or prioritized, risk mitigation strategies need to be developed, created, or designed. This requires detailed analysis and discussion with team members, stakeholders, and subject matter experts.
5. Deploy Uncertainty Reduction Mechanisms Once risk mitigation strategies have been developed, created, or designed, they need to be implemented, activated, or deployed. This requires collaboration and coordination among team members, stakeholders, and subject matter experts.
6. Update Uncertainty Reduction Mechanisms Risk management is an ongoing process that requires continuous monitoring, review, and improvement.
Benefits of Effective Uncertainty Management in Lean Six Sigma Projects
Effective uncertainty management in Lean Manufacturing Six Sigma projects offers numerous benefits, including improved project outcomes, increased efficiency, and enhanced stakeholder satisfaction.
In conclusion, risk management is an essential process that aims to eliminate waste and optimize efficiency. It ensures that projects are completed on time, within budget, and to the required quality standards. Effective risk management requires collaboration and coordination among team members, stakeholders, and subject matter experts.
Reviews