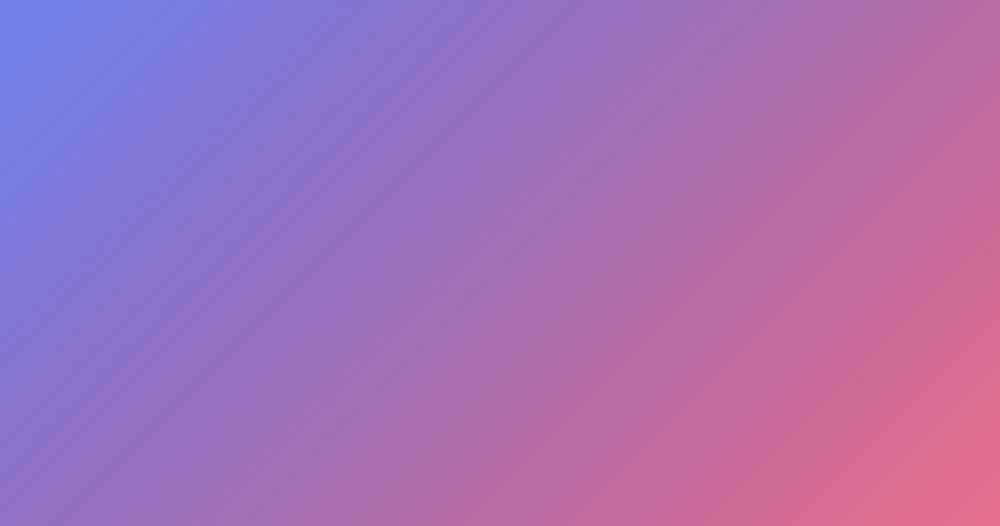
13
abrilDiscovering Deeper Issues for Deeper Problem Understanding
Applying the 5 Whys method using a deeper problem understanding has been a common practice in several decades, especially within the confines of the Lean and Six Sigma methodologies. This problem-solving technique employs repetitive questioning of a question to drill down to the root cause of an issue.
To successfully apply the 5 Whys method, it is vital to observe and ask follow-up questions in the most independent perspective possible. Each subsequent question also needs to delve more under the layer of the issue observed, usually assuming that the final question's answer represents the root cause of the observed problem.
The process of 5 Whys question-asking usually initiates with a major complaint presented by a team colleague, a customer, or some outside event. The method views this primary complaint "{The 1st Why|The Initial Inquiry|The Primary Question." The problem needs to be analyzed, and a deeper understanding of the situation has to be gained. This deeper understanding is then {explored|investigated|examined} by asking "Why" multiple times until the correct root cause of the issue becomes evident.
For example, {assume|suppose|hypothetically} an employee observes a customer complaint, saying that their received shipment package arrived damaged. In this case, the initial problem presented can be set as "the package arrived damaged." At this stage, the "Why" needs to be observed: "Why did the package arrive damaged?" The key is to figure out the correct contributing or single root reason that would contribute to the observed problem.
The {subsequent|following|next} query may be "Why was the packaging {insufficient|inadequate|incomplete} for shipping?" Because upon repeated "Why" questioning, this is the reality of what likely occurred. Next, it is easy to derive why the packaging specifications were {improperly|incorrectly} finalized. By additional "Why" questioning, the root can {typically|usually|generally} be very obvious: a lack of {communication|information|collaboration} about necessary packaging dimensions required 5S for improvement shipping.
By {practicing|implementing|utilizing} the 5 Whys technique regularly, it is {possible|feasible|achievable} to {encourage|promote|foster} objectivity, grow empathy, and {raise|increase|enhance} the level of insight into each team {member|colleague|associate}. One should {establish|create|develop} an enduring improvement within one's company by understanding that the most pressing issues confronted {require|demand|need} effective problem-solving inquiry, the identification of the root causes, and an {analysis|examination|evaluation} and removal of the main source of the issue.
Reviews